Thursday, January 12. 2017
#1: Be able to drive (obviously) and be able to press the button on the hopper (which are boxes on the edge of the field) that releases the green fuel balls onto the field.
#2: Store about 20 fuel balls, gather fuel from the field, score fuel into the high goal of the boiler from the Key (check out the picture below for reference as to where that is), and pick up a gear from the driver station and deliver it to the airship.
#3: Gather fuel from the driver station.
#4: Climb the rope.
#5: Score high goals from by the airship.
#6: Lowest on the list, score fuel into the low goal of the boiler from the Key
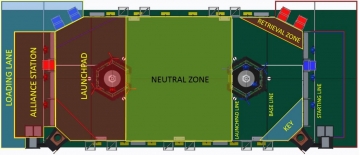
Let’s check them out!
(Please keep in mind that these are only prototypes, and that we may not use these ideas in our final robot)
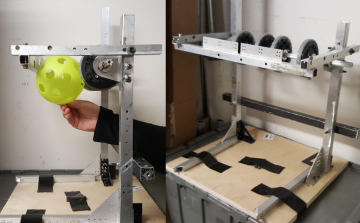
The wheels on the high shooter spin at high speeds to shoot the fuel into the high goal of the boiler, which is a little over 8 feet high. It’s designed to shoot several fuel at the same time, but the shots will be slightly staggered so that they don’t hit each other in mid-air. It sounds simple, but so far we have had problems getting the wheels to spin fast enough to shoot the fuel to the height we need.
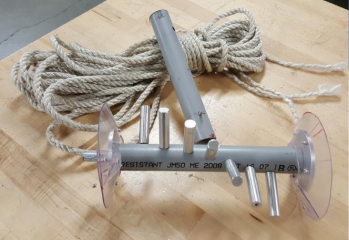
Our climber is a tube with small metal bars sticking out from it. To help us climb, it will start spinning, catch a loop that we are putting on the bottom of our rope, and twist the rope around itself while simultaneously pulling the robot up.
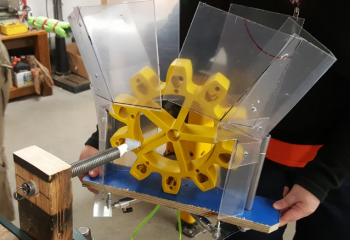
This prototype acts as a ‘pocket’ to hold the gears while transporting them, and is able to push the gear onto the peg that carries it up onto the airship. The mechanism is made of mostly Lexan and has two doors controlled by pneumatics so that it can leave the gear on the peg and drive away.
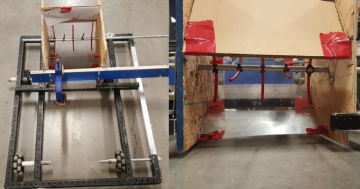
“The Chicken Plucker”, our intake system, spins pieces of pneumatic tubing that catch the fuel balls that are scattered across the field, and brings them into the robot.
It is mounted in a prototype of our drivebase, the style of which has been hotly debated over for the last couple of days. On Wednesday night, we finally settled on a West Coast style of drivebase, which has wheels on the outside of the frame (unlike the drivebase pictured above) which are directly driven by the transmission. Since the wheels aren’t taking up space on the inside of our frame, this leaves us more room to work with on the inside of our robot.
This year there are two different volumes our robot could be: either 36 in. x 40 in. x 24 in. tall or 30 in. x 32 in. x 36 in. tall, and it can weigh up to 120 lbs. We will decide which volume to use once we finalize the mechanisms we are using for the shooter, intake, etc. But for now, our CADers have created some initial designs so we can start planning out where everything will fit in the robot:
Someday, it will hopefully look more like this:
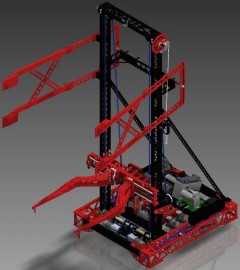
Tonight we are making some serious decisions on our final robot design, including what prototype designs we’re going with and which size of robot we will be using. We will report back sometime this weekend with all of our plans.
40 days until Stop Build Day!
-Student Blogger Katie